Extrusion and profile design
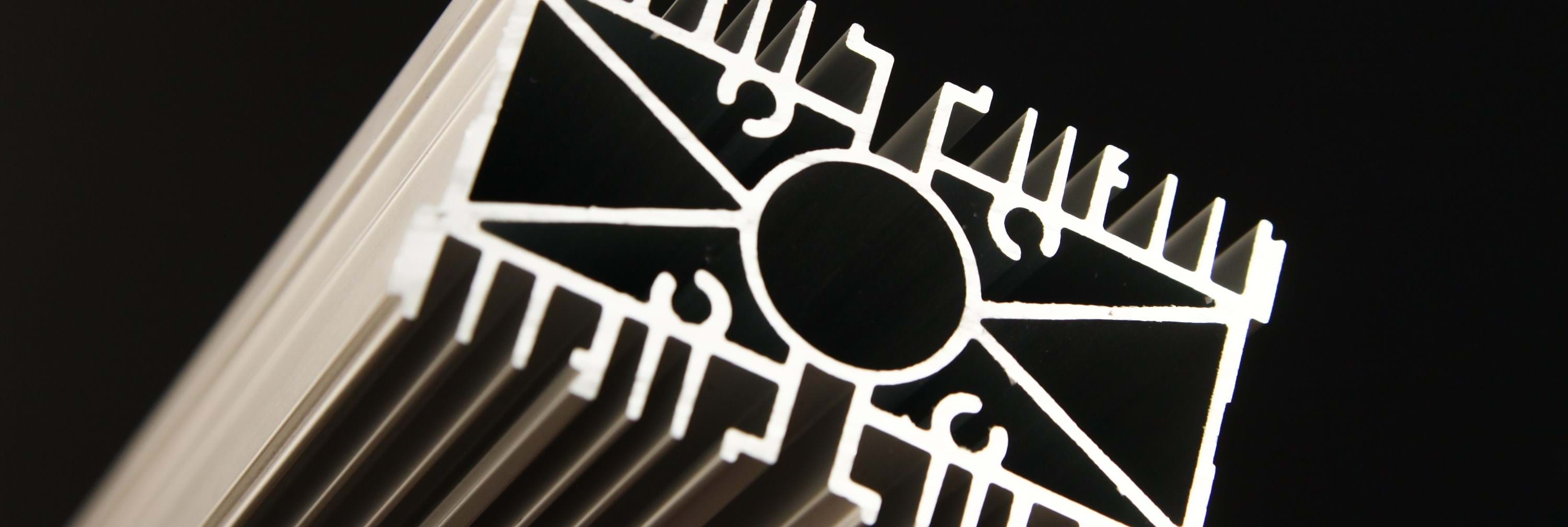
A key advantage of aluminium is that it can be extruded as profiles. This opens a wide range of design possibilities that make aluminium unique in an industrial context.
On this page you will find more information about profile extrusion, prototypes and design tips.
/
What is extrusion?
Extrusion can be compared to squeezing toothpaste out of a tube. The hot, soft aluminium billet is forced through a tool in a specific shape, just like the round opening on the toothpaste tube. Extrusion is used for both custom profiles and standard profiles such as square bars and round tubes.
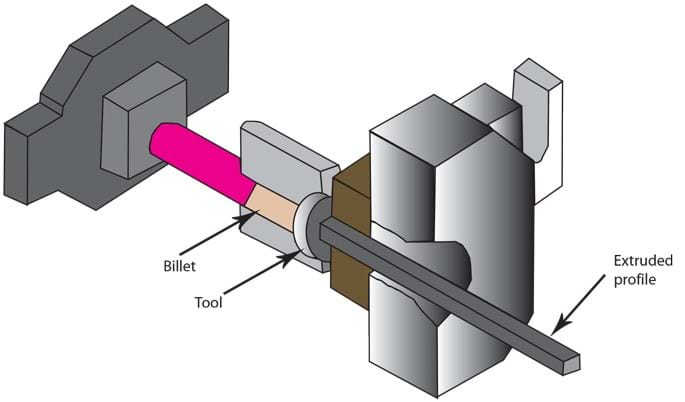
The billet is heated to 450-500°C before extrusion. The melting point of aluminium is approximately 660°C, so the billet is soft, but not liquid.
When the profile comes out on the other side of the die, it is cooled with water or air.
The profile is then stretched while still soft to release stresses in the metal and achieve the correct dimensions. Finally, the profiles are treated by either cold or hot hardening to achieve the defined strength/hardness before anodising or painting, if required, and cut to the correct lengths.
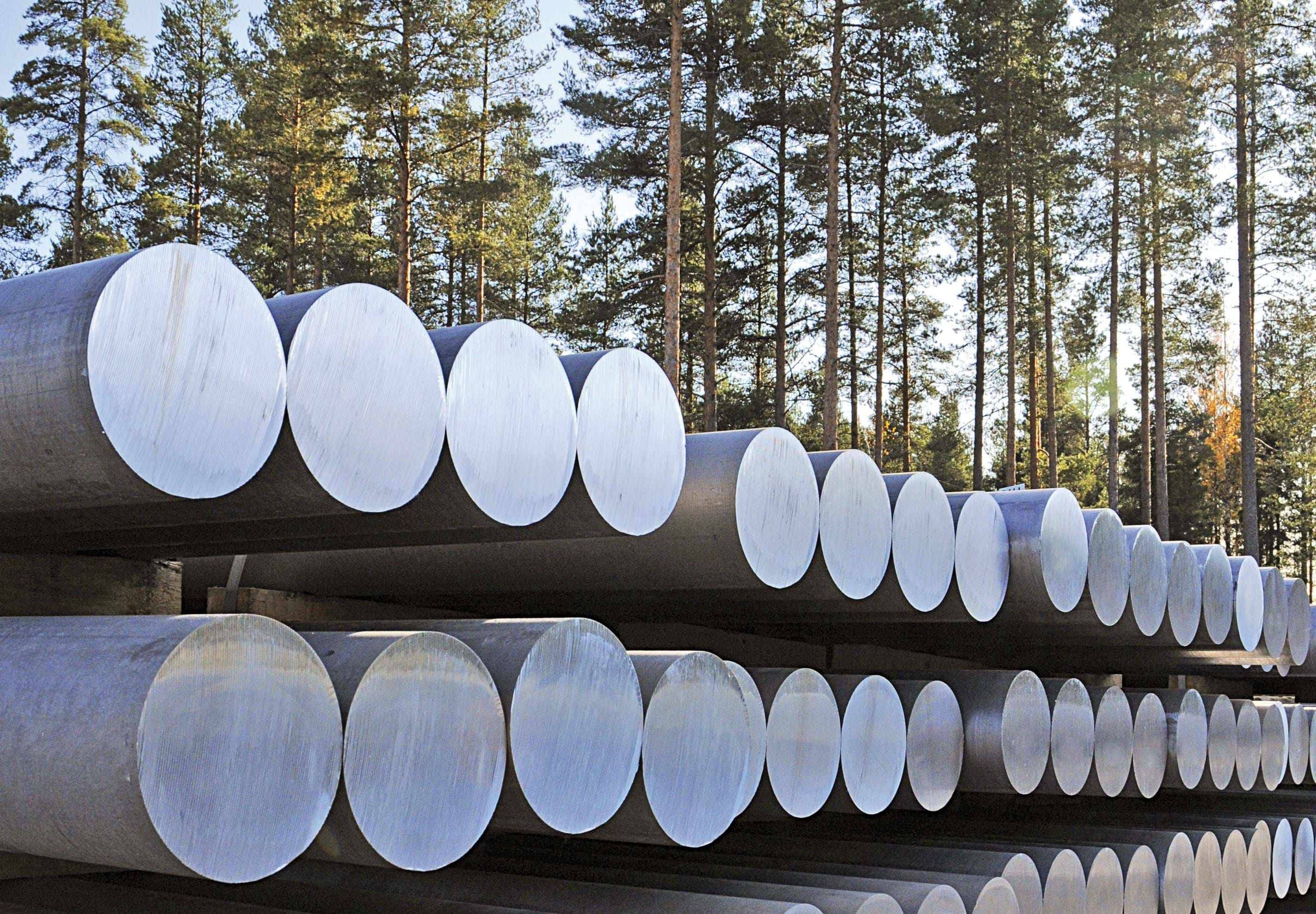
Extrusion is relatively economical because it is easy to produce large quantities in a short time. Once you have the die, it can be used for several batches of the same profile.
Extrusion of custom profiles
Extrusion of special profiles requires a die, which the aluminium billet is then extruded through.
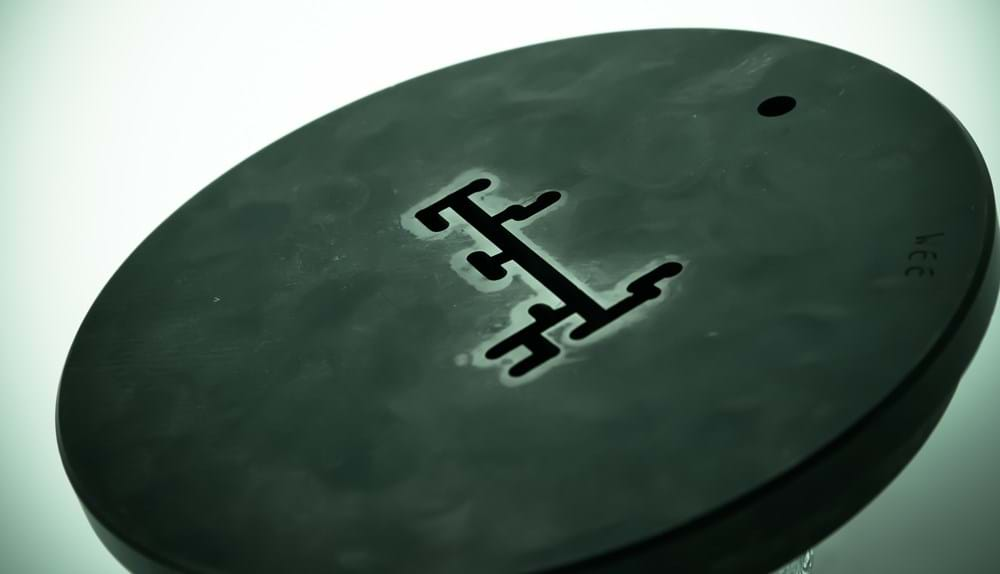
The die is designed specifically for each (non-standard) profile. Designing and producing the die for custom profiles poses an initial cost – but once the die is designed, it can be used over and over again.
To minimise costs, it pays to think through the design before you start production. For example, you can incorporate features such as screw channels and click functions into the extrusion to make finishing, machining and assembly as easy as possible.
Solid profiles can be extruded with a single tool, while hollow profiles require a two-part tool. One part forms the outer mould of the profile, while the other part acts as a core that creates the cavity in the profile.

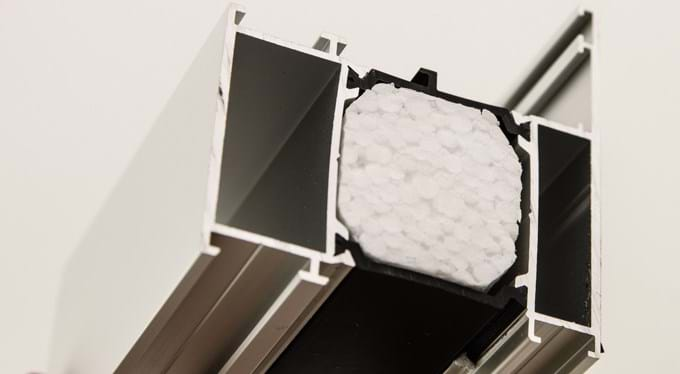
Aluminium has a high thermal conductivity, which can cause problems in structures that are in contact with two different environments at the same time. A common example would be facade profiles or windows in pure aluminium that connect a cold outdoor environment with a warmer indoor environment.
If the cold is conducted through the profile, thermal bridges can occur and lead to condensation in the construction.
Therefore, extruded profiles can be supplied with built-in insulation.
The insulator is typically polyamide, which is fitted between two profiles shortly after extrusion.
Design for extrusion
Although extrusion is a very flexible production method, there are certain design requirements. With a few simple ground rules, you can design a profile that will be extruded as accurately as possible and will stand the test of time.
Here are a few selected examples of typical problem that you can easily avoid. The table is a simplification, so we always recommend that you contact us as early as possible in the idea phase for guidance.
To prefer | To avoid | Comments |
![]() ![]() |
![]() ![]() |
Arrange hollows symmetrically, if possible. |
![]() ![]() |
![]() ![]() |
Open screw channels show a better geometrical accuracy in relation to each other and give a longer life to the die. |
![]() ![]() |
![]() ![]() |
Peaks should be rounded (avoid filling problems; higher extrusion speed). |
![]() ![]() |
![]() ![]() |
Narrow slits only if unavoidable, otherwise add spacers whereby the tolerances of the opening distance are considerably improved. |
![]() ![]() |
![]() ![]() |
Contours which are connected with an unfavourable flow of material reduce extrusion speed and induce tolerance problems (for the cross section as well as for straightness and torsion). |
![]() ![]() |
![]() ![]() |
The tolerances for polygonal formed open cross sections can be improved considerably by adding stiffeners or by designing a hollow section. |
![]() ![]() |
![]() ![]() |
Small geometries of a thick section are difficult to fill out with metal and sometimes cannot be extruded. |
![]() ![]() |
![]() ![]() |
Small appendices in connection with thick parts of a section are hard to fill with metal and sometimes cannot be extruded. |
![]() ![]() |
![]() ![]() |
Avoid too thin or too wide walls in hollow sections (problems with tolerances, increased waste since defect not repairable). Arrange supporting spacers. |
Thomas Gork, technical consultant, Alumeco
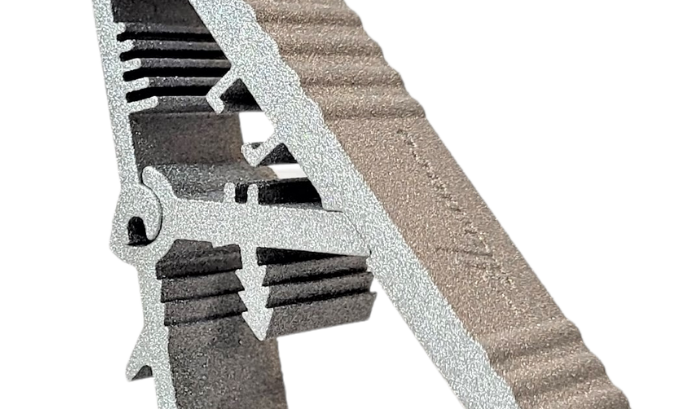
3D printing in metal saves you the trouble and cost of developing a die for extrusion, and you only consume the material that the part itself requires - there is no waste.
For prototyping, 3D printing in metal provides virtually the same properties as final extrusion.
With 3D printing, we can produce very complex parts with low tolerances and there are design advantages compared to extrusion.
For example, you can design cavities in an otherwise solid part, minimising weight and material consumption.
At Alumeco, we offer 3D printing in plastic, aluminium, stainless steel, titanium and copper. We deliver metal prints in sizes up to 400 x 400 x 360 mm and the delivery time is 10 days.